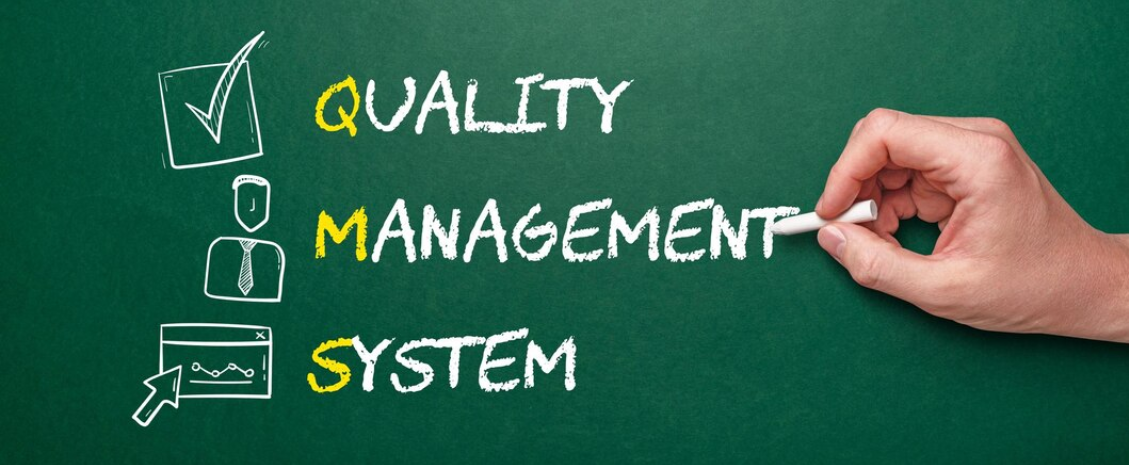
Posted on: Jun 06, 2024
A Quality Management System (QMS) is an organized framework that details processes, procedures, and responsibilities to fulfil quality policies and objectives. It helps coordinate and direct an organization’s activities to meet customer and regulatory requirements, consistently improving its effectiveness and efficiency. Implementing a QMS is crucial for maintaining high-quality products and services and impacts every aspect of an organization’s performance, offering numerous internal and external benefits.
Among all the benefits that QMS brings, the following can be distinguished in the first place:
1. Customer Satisfaction:
Quality management ensures that products or services meet or exceed customer expectations. Satisfied customers are more likely to become repeat customers, provide positive reviews, and recommend the business to others.
2. Consistency and Reliability:
Implementing quality management processes helps ensure that products and services are consistent and reliable, reducing variability and defects. This consistency builds trust with customers and stakeholders.
3. Cost Efficiency:
Effective quality management reduces waste, rework, and defects, leading to cost savings. It helps optimize resources and minimize unnecessary expenditures, which can significantly impact the bottom line.
4. Compliance and Risk Management:
Quality management helps ensure compliance with industry standards, regulations, and legal requirements. This reduces the risk of non-compliance penalties, legal issues, and reputational damage.
5. Competitive Advantage:
High-quality products and services can differentiate a business from its competitors. A strong reputation for quality can attract more customers and create a competitive edge in the market.
6. Employee Engagement and Morale:
A focus on quality management often leads to improved processes and a better working environment. Employees who are involved in quality initiatives feel more valued and are more likely to be engaged and motivated.
7. Continuous Improvement:
Quality management fosters a culture of continuous improvement. By regularly assessing and improving processes, products, and services, organizations can adapt to changing market conditions and innovate more effectively.
8. Reputation and Brand Image:
Maintaining high quality standards enhances the reputation and brand image of a company. A strong reputation for quality can attract new customers, retain existing ones, and facilitate partnerships and collaborations.
9. Operational Efficiency:
Quality management practices streamline operations, reduce bottlenecks, and improve overall efficiency. This can lead to faster delivery times, better resource utilization, and higher productivity.
10. Market Expansion:
Quality certifications and adherence to international standards can open up new market opportunities. Companies with robust quality management systems are often preferred suppliers in global markets.
11. Financial Performance:
Consistently delivering quality products and services can lead to increased sales, higher customer loyalty, and better financial performance. Quality management contributes to long-term profitability and business sustainability.
How to implement Quality Management in the Organization?
1. Define Quality Objectives and Goals
Set Clear Quality Objectives: Establish what the organization aims to achieve in terms of quality. These objectives should be specific, measurable, achievable, relevant, and time-bound (SMART).
Align with Organizational Goals: Ensure that quality objectives align with the overall strategic goals of the organization.
2. Develop a Quality Management System (QMS)
Choose a Quality Framework: Select a quality management framework or standard, such as ISO 9001, Six Sigma, or Total Quality Management (TQM), that best suits the organization’s needs.
Document Processes and Procedures: Create detailed documentation of processes, procedures, and work instructions that define how quality will be managed and maintained.
3. Leadership Commitment
Top Management Involvement: Ensure that top management is committed to quality and actively participates in quality initiatives. Leadership should provide clear direction, resources, and support.
Quality Policy: Develop and communicate a quality policy that reflects the organization’s commitment to quality.
4. Employee Involvement and Training
Engage Employees: Involve employees at all levels in quality management. Encourage participation and feedback to foster a culture of quality.
Provide Training: Offer training and development programs to equip employees with the skills and knowledge necessary to maintain and improve quality.
5. Process Management and Improvement
Process Mapping and Analysis: Identify and map key processes within the organization. Analyse these processes to identify areas for improvement.
Continuous Improvement: Implement continuous improvement methodologies such as PDCA (Plan-Do-Check-Act), Lean, or Kaizen to systematically improve processes.
6. Quality Control and Assurance
Implement Quality Control (QC): Establish quality control procedures to monitor and measure product and service quality against defined standards.
Quality Assurance (QA): Develop quality assurance processes to ensure that quality is built into every stage of the product or service lifecycle.
7. Measurement and Monitoring
Set Key Performance Indicators (KPIs): Define KPIs to measure quality performance. These could include metrics such as defect rates, customer satisfaction scores, and process efficiency.
Regular Audits and Reviews: Conduct regular internal and external audits to ensure compliance with quality standards and identify areas for improvement.
8. Customer Focus
Understand Customer Needs: Gather and analyse customer feedback to understand their needs and expectations.
Customer Satisfaction: Implement processes to monitor and enhance customer satisfaction.
9. Supplier Quality Management
Select and Evaluate Suppliers: Choose suppliers based on their ability to meet quality standards. Regularly evaluate supplier performance and work with them to improve quality.
Supplier Partnerships: Develop strong partnerships with suppliers to ensure quality throughout the supply chain.
10. Documentation and Record-Keeping
Maintain Records: Keep detailed records of quality management activities, including audits, inspections, and corrective actions. Ensure documentation is accessible and up-to-date.
11. Risk Management
Identify Risks: Identify potential risks to quality and develop mitigation strategies.
Risk Management Plan: Implement a risk management plan to proactively address and manage risks.
12. Review and Continuous Improvement
Management Reviews: Conduct regular management reviews to assess the effectiveness of the QMS and identify opportunities for improvement.
Feedback Loop: Create a feedback loop where lessons learned and improvement suggestions are continuously incorporated into the QMS.
In summary, quality management is crucial for ensuring customer satisfaction, achieving operational excellence, and maintaining a competitive advantage. It supports the reliability, efficiency, and reputation of an organization, ultimately leading to sustained success and growth.
Author:
Izabela Henke
Senior Project Manager & Senior Consultant